INTRODUCTION
After reading the title of the blog, the first question that must have popped into your mind be:
CAN YOU PRINT ONTO A GLASS?
Well, the answer is
YES!
You might be surprised to know that screen printing on glass is one of the most widely used methods in packaging. Single-colored or multi-colored it can be done in both types. This blog describes the unknown benefits of glass screen printing and thoroughly explores the whole process.
Let’s read further!

WHAT IS SILK SCREEN PRINTING ON GLASS BOTTLES
Screen printing is a method of selective layer deposition of a specific material on flat surfaces. The material passes through a textured screen during the printing process. This screen printing on flat glass surfaces is known as screen printing on glass.
Silk screen-printed glass refers to a float glass decorated by screen printing. For the application of frit during screen printing, three different patterns are used:
- Dots
- Lines and
- Empty gaps or across the whole surface
The end product can be transparent, translucent or opaque. However, it depends upon which technique is used. Combining a large range of basic glass and various colors gives the makers a big room for creativity.
HOW IS SCREEN PRINTING ON GLASS BOTTLES DONE
The word screen printing might seem simpler, but the process is complex. It is a very difficult and time-consuming process. Screen printing on glass requires not just time but also a lot of expertise. Let’s look at the process step by step in detail.
- DESIGN
The preliminary step is the creation of the design. It is better to create a simple design with just a few lines. Simple colors should be used. Try using colors that best identify with the brand identity. Take a transparent acetate film and print the design on it.
- SCREEN
The next step is the preparation of the screen. Identification of the correct screen mesh is important. The screen mesh selection depends upon the glass bottle’s thickness and the desired design. Then, evenly coat the mesh screen with a light reactive emulsion.
- EXPOSE THE EMULSION
Now, place the acetate film on the coated mesh screen. Because emulsion is reactive to light, the design will remain liquid, and all other areas will become hard. If the design is multi-colored, you will need a separate screen for each color.
- STENCIL
Once the emulsion step is complete, dip the screen in water for about sixty seconds. Make sure the water is at room temperature. Rinse and wash any emulsion that did not become hard when exposed to light. After the mesh dries, make necessary adjustments to ensure the stencil is close to the original design.
- THE INK
Prepare the ink after the stencil is ready. Mount the mesh screen on the printing press with the glass bottle under it.
- PRESSING THE INK
Keep adding ink to the screen board top. For an even spread, use a squeegee. This pushes the ink through the forged areas of the stencil onto the glass bottle. Thus impressing the image on the glass bottle.
- DRYING PROCESS
The last step is the simplest of all. It’s simply all about giving ample time to the glass bottle to heal, i.e., drying up.
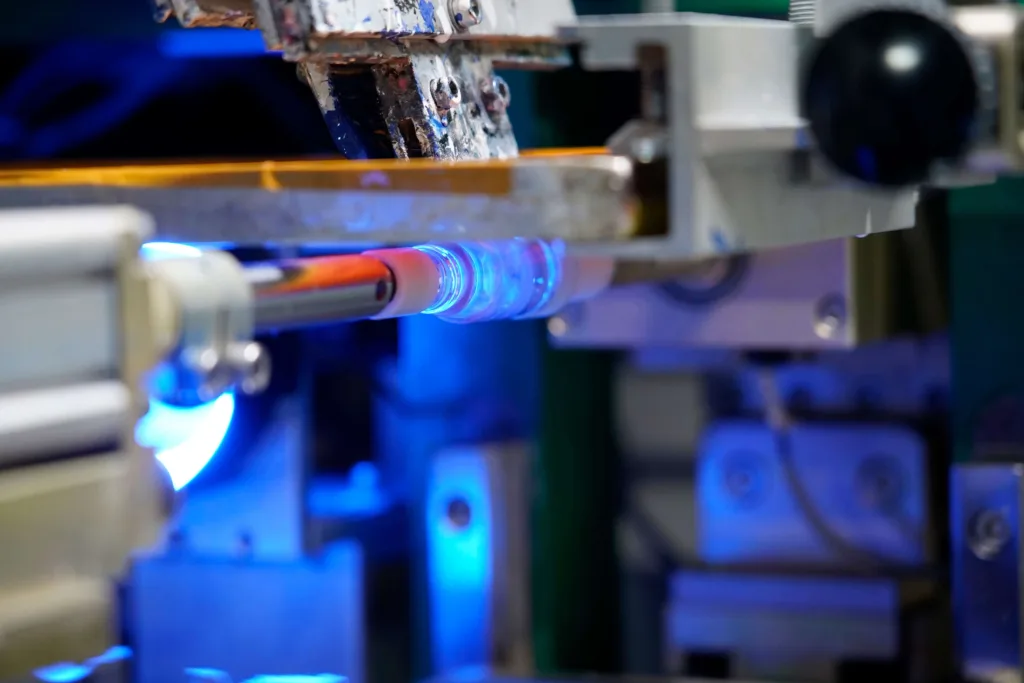
CHALLENGES YOU MIGHT FACE DURING THE PRINTING PROCESS
The screen printing process is challenging. Glass screen printing is also not an exception. Let’s have a look at the challenges in performing glass screen printing
- In the absence of adequate drying time, the prints might become sticky. Therefore, it is better to make sure that you give sufficient drying time for your final product.
- Another major challenge that you might face is ink cracking or paint peeling. This occurs on the surface of the bottle. The reason behind this problem is improper curing time. Provision of adequate curing time at the appropriate temperature is therefore necessary.
- Paint washing is A very important issue during the glass printing process. When not provided enough curing time, the paint might wash away from the surface of the glass bottle.
From the before mentioned challenges, curing at the right temperature is crucial to screen printed glass perfectly. Therefore, makers should ensure the final product is given ample time to dry.

BENEFITS SCREEN PRINTING ON GLASS BOTTLES
- REUSABLE AND DURABLE
Screen-printed glass can endure many washes. This makes screen-printed glass products not just reusable but also more durable. The design remains intact no matter how often you use or wash the product.
Therefore, when customers can reuse the products, they will purchase more. Loyal customers might bring more customers through word of mouth. Such durable products will make the overall business model budget-friendly and environmentally friendly.
- BYE BYE COMPETITORS
It would be best to make your product unique to stand out from your competitors. These days, customers are more informed. They prefer style and creativity. Therefore, unique packaging and printing can greatly impact consumers’ purchase intentions.
Screen printing on glass is not just a unique way of communicating brand identity, but it is also creative. You can make use of as many colors as you want. You can use unique colors and techniques to make the printing more creative. These techniques include glow-in-the-dark and precious metals.
The environmentally friendly feature of the glass bottles can attract consumers who are fond of burning eco-friendly products.
- TARGETING THE “HIGH QUALITY MIND SET
You must have heard that “first impression is the last impression.”
That’s true!
When customers see a product for the first time, the product packaging makes the first impression. You might lose a customer if the product packaging needs to be done right.
Glass screen printing provides a unique finish and a creative look to the product. Customers assess the quality of the product through its packaging.
Therefore, good-quality glass printing gives the product a high-quality look. Since high quality is what the customer wants through glass screen printing, you might be able to target the HIGH-QUALITY MINDSET of the consumers.
- PERSONALIZATION OF PRODUCTS
Customized products are always in huge demand. Customers are always willing to pay more for the product that matches their demand and desires exactly.
Glass screen printing can be used to personalize products. This can be done by using printing colors which the customer demands. Personalized perfumed bottles are a good example.
Brands can create a customer tailored range of perfumes. Customers can share their font and color ideas with the vendor. Customized perfume bottles can be created using glass screen printing method.
CONCLUSION
Glass screen printing is no doubt a challenging process. It, however, seamlessly blends product labeling and packaging. The durability and reusable feature of the product after being screen printed adds to its attraction. The glass screen printing process might be difficult, but the result and impact are long-lasting.