Introduction
Pad printing represents a solution to the growing customization demands in the perfume bottle printing and packaging industry. Increased customization demands the printing and labeling of vibrant colors, high-resolution images, and attractive labeling options. Such printing is a way to attract more customers to the perfume bottle.
Pad printing is a convenient and cost-effective option for low-volume perfume manufacturers. They are ideal for a small manufacturing setup and are scalable as well.
Suppose you are looking for an affordable printing and customization option for your perfume business. In that case, this blog is for you. It explains all the important details about pad printing along with the advantages and disadvantages.

What is Pad Printing?
Also known as tampography or tampo printing, pad printing is an affordable printing and labeling technique. It transfers a 2D image onto a 3D object or surface. The 2-D image is first printed on a cliché. A cliché is a laser-engraved printing plate. With the help of a silicon pad, the image is transferred from the cliché to the 3-D object or surface.
Pad printing is quite different from traditional printing techniques. It is because it can label curved spherical and cylindrical surfaces and objects. Traditional printing techniques could not label or print 3-D surfaces or objects.
For the labelling of custom perfume bottles pad printing is a very common technique. Many perfume bottle manufacturers prefer pad printing over other labeling options. The reasons for their preferences will be elaborated later in this blog.
Previously, pad printing was used to print crockery items. It was a simple manual process with limited design and color options. The advancement in the printing machine led to the automation of the process. Manufacturers started using this process for the labeling of products. In the early days, the design was transferred to the object using soft gelatin. Later, soft gelatin was replaced by a silicon pad.
Also, the use of steel and iron clichés with laser-engraved designs resulted in unlimited design and color options. The automation of the process made it less time-consuming and more efficient.
Components for Pad Printing
Although the pad printing process appears to be very simple, implementation involves several components. In this section, we shall look at all the essential components required to implement the pad printing process successfully.
Pad Printing machine
Of course, the most important component of the pad printing process is the pad printing machine. There are further three classifications of the pad printing machine which are:
- Closed ink-cup
- Rotary gravure
- Open ink well
These three printing machines has different setups. Also, they all have different printing styles. The most versatile of all three methods is the open inkwell printer. This printing machine uses a spatula and a doctor’s blade. The spatula floods and spreads the ink on the blade.
The closed ink cup printing machine stores the printing ink in a printing cup. This is the most universal pad printing method.
Although the rotary gravure is similar to open ink, it is well functioning and set up; what makes it unique is its ability to rotate on the printing object around 360 degrees.
The Printing Plate
A major component of the pad printing machine is the printing plate. As discussed before, a printing plate is the one that holds the design before it is transferred to the printing object. These printing plates are made of Plastic-plastic or thin metals.
The use of these printing plates is a major factor in making the pad printing process more convenient, cost-effective, and flexible. Printing plates made of steel are more durable and more useful for large-scale productions. Printing plates are further of two types, which are as follows:
Laser Plate-Making
This process uses a laser marking machine to engrave the labeling design onto the printing plate. Laser marking machines create designs that are precise and accurate. They are also very high in resolution. Laser plate making is a very fast and efficient process.
Because of the use of a laser marking machine, you can create images and designs within minutes. Also, this process allows immense flexibility in design. You can create variable designs with variations in depth, pattern, and quality.
Photopolymer Plate Making
As the name implies, the photopolymer process involves the use of UV lights. In this process, the printing plate is exposed to UV lights unless the design is completely etched on it. This process is more time-consuming as compared to the laser plate-making process.
Pad Print Ink Cup
You might have some idea about the name of the component. The pad print ink cup consists of two main parts. These are the cup and the ring. The cup stores the ink inside. The main purpose of the ring is doctoring the ink onto the surface of the printing plate. As the rink does the doctoring, the inks get transferred from the cup to the surface of the printing plate.
The ring is made of either ceramic, Plastic Plastic, or metal. Among all three materials, ceramic is the ideal one. It is because of its ability to move on the plate without creating any scratches. It also has the ability to manage and handle the constant motion of the pad printing machine.
Printing Inks
If you have all the pad printing components but not printing ink, then everything else will go to waste. Pad printing inks consist of three main components which are:
- Resins
- Thinners
- Pigments
Each component of the pad printing ink has a specific property and advantage. The thinner maintains the viscosity of the ink. The pigments give the color. The resins add to the mechanical properties of the pad printing inks. They make it less abrasive and more resistant to scratches and adhesions.
For good results, it is better to choose the most suitable ink for your industry. It would help if you made a datasheet of the properties you are looking for and then choose accordingly.
Printing Pad
The printing pad is the component that transfers the design onto the object from the printing plate. Its functioning is very simple.
- The printing pad first compresses itself on the printing plate. As a result of this compression, the design from the plate is transferred to the printing pad.
- It then slides over to the object and compresses again.
- The design gets transferred from the pad to the surface of the object.
- The forming material of the printing pad is silicon.
How to do Pad Printing on Perfume Bottles
Intricate shimmery patterns or opaque vintage designs, you can create it all using the pad printing technique. However, you might have some idea of the pad printing process from the information listed up till now. However, in this section, we shall explain the pad printing process exclusively for perfume bottle labeling.
Remember that pad printing is an amazing idea to brand your perfume bottles.
Creating Digital Illustrations
Whether you are manufacturing a product or packaging it, designing is the first crucial step of the process. The same is the case with labeling perfume bottles. When printing a pad, you first design the label using a digital illustration.
You need to create a logo or sticker that best describes your brand. For this purpose, you can hire a graphic designer as well.
Making of a Customized Cliché
Making a customized cliché is the next step in pad printing a perfume bottle. The cliché is developed in accordance with the digital design or illustration.
Filling the Cliché
This step involves the use of special inks. These special inks fill the cliché. It is important that the cliché and the ink colors are exactly in accordance with the digital illustration. Otherwise, the label would be different from the inspired design.
Transferring the Design onto the Perfume Bottles
In this step, a gentle pad transfers the design from the cliché to the surface of the perfume bottle.
Getting Optimal Outcomes
Just like any other process, the pad printing process also needs to achieve optimal outcomes. For this purpose, sampling is important. As a perfume bottle manufacturer, you can give a few empty bottles to the pad printing company to create sample imprints on them. Choose the one that best suits your requirements to attain optimal performance.
Advantages
This section analyzes the advantages pad printing offers to perfume brands and manufacturers. Let’s have a look at them one by one.
Offers Customization
Pad printing offers a variety of customization options. The major reason for this is that pad printing works well with several material types and colors. You have a variety of labeling and printing design options with this technique.
Versatile Technique
Not only is pad printing compatible with various materials and colors, but it also goes well with different surface shapes. Since perfume bottles come in a huge variety of shapes and sizes, it is sometimes difficult to print on curved surfaces. Pad printing has resolved this issue. It can easily be applied to curved surfaces and a variety of shapes.
Efficiency
Pad printing is more practical for small business owners because of its cost-effectiveness. However, it is efficient enough to be used by larger businesses as well. It is an efficient process that does not require any complex machinery, raw materials, or tools.
Precision
Pad printing makes designs and prints that are precise and accurate in dimensions. Dimensional accuracy adds to the favor of the technique. It allows the perfume brands to print high-resolution and high-quality prints on perfume bottle surfaces, no matter whether they are curved, intricate, or flat.
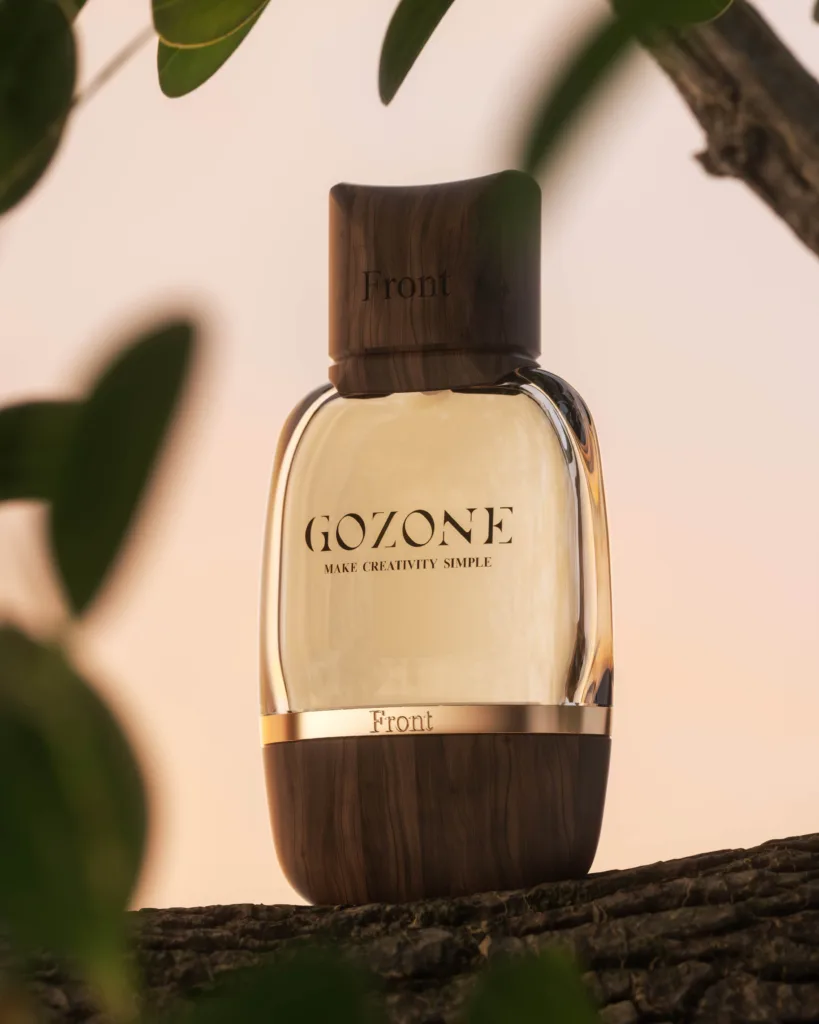
Limitations
This section explains the limitations associated with the pad printing process. Let’s dive into the details to analyze the suitability of pad printing for perfume brands.
Not for the Amateurs
The pad printing technique might seem simple, yet it is only for some amateurs. Before starting the princess, you need to have at least some basic understanding of how labeling and printing work. Remember that it is not “black art.” That is why it is always recommended to hire an expert for pad printing your perfume bottles.
Expected life of Consumables
This technique involves several components. Be it the cliché, the inks, the silicon pad, etc. These are all consumable components and might need replacement after some time. Using wear-out components can affect the quality of the print. The expected life of consumables expectancy is low.
The use of plastic
Pad printing, although widely used by both small and large businesses, poses certain hazards to the environment. It is because it uses plastics. Polyethylene and polypropylene plastics are used in the process, making it less environmentally friendly.
However, this hazard is only in the case of printing on plastics because these polymers provide adhesion. In the case of glass perfume bottles, there is no such hazard.
Selecting the Ink and Pad
Selecting the right ink for the right substrate is important. It would help if you were an expert yourself, or you should see the guidelines of an expert. This is the main reason why making or sharing a sample before labeling the whole order is highly recommended.
Pad Printing or Sticker Labelling?
This section explains the difference between two popular perfume bottle labeling techniques, i.e., pad printing and sticker labeling.
Factors
Pad Printing
Sticker Labelling
Print Quality
This offers luxurious and high-resolution printing options. The quality of prints and labels could be better than that of pad printing.
Updating
You cannot replace a label with pad printing. Once printed, it is not viable to remove it from the surface. Sticker labels are easy to update and replace. If you don’t like it, remove it and replace it with the one you like.
Investment
This requires a bigger financial investment than sticker labeling. This requires less financial investment than pad printing.
Surface Suitability
This technique is versatile. You can apply it on all shapes, i.e., flat or curved. This technique is limited to flat surfaces only.
Conclusion
Perfume brands these days focus a lot on quality and customization. Because these two factors act as magnets for customers. Pad printing, being the more durable and better-quality option, takes the edge on sticker labeling in the case of perfume bottles. However, a major constraint is budget. Before making the actual choice, you need to consider your budget and, of course, expertise.