CNC machines are popular because they produce minimum errors. This quality makes them the perfect tools for manufacturing machining parts that require minimum error and deviations. You will be amazed that the probability of error in CNC Machining is less than 1 percent. However, the achievement of this probability is possible only because of the presence of skilled labor, efficient machinery, and continuous quality control measures.
This blog explains different quality control and quality assurance methods that ensure the manufacturing of accurate machining parts with minimum deviations from standard measurements. It also explains the various tools that measure the manufactured parts and the main parameters against which the manufactured parts are measured and compared.
Quality Control and Quality Assurance in CNC Machine
Quality testing and quality inspection are two different processes but have the same purpose. In the CNC Machining process, both processes ensure that the outcome is in compliance with the standards of accuracy and integrity. Both methods ensure that every CNC Machining component is aligned with precise specifications.
Quality control and quality inspection are responsible for maintaining high production standards in CNC Machining, whether through material analysis or quality control checks.
1. Quality Control
Quality testing or quality control involves several techniques and instruments. Its basic purpose is to identify and reduce errors during the manufacturing process. It also ensures that the components manufactured through CNC Machining operations comply with the manufacturing and regulatory standards of production.
Failure to comply with quality testing techniques results in errors and losses. These include the manufacturing of defective components. The main control of quality testing or control is towards the operational side of CNC machines for metal. It pays more attention to the product and is a reactive approach.
2. Quality Assurance or Quality Inspection
The quality assurance process occurs after the quality testing process. Its purpose is to inspect whether the manufactured components are in accordance with the specified production criteria. It inspects based on precision and accuracy.
Quality assurance is a proactive approach. It pays more attention to the manufacturing processes than to the product itself.
Quality assurance ensures that production processes are accurate and efficient enough to produce precise components.
Major Parameters of Quality Testing or control in CNC Machining Operations
1. Dimensional Accuracy and Tolerance
Dimensions play a critical role in CNC machine operations. You must get even the slightest dimensions right to ensure the usefulness of your manufactured components.
This is why measurement checks are an integral part of quality control activities. This is true, especially in high-precision industries such as defense and aerospace.
Both dimensional accuracy and Tolerance are critical parameters of quality control.
As the name suggests, dimensional accuracy indicates the alignment of the product’s actual dimensions with the specified measurements.
Tolerance, on the other hand, is the least level of permissible variation in the measurements of the finished product. It indicates how much the actual product can deviate from the specified measurements.
To ensure that the products align with the quality control parameters, you can use several instruments. These include a CMM, a coordinate measuring machine, calipers, and micrometers.
In the case of a CNC machine, accuracy does not just align with the specified measurements. It also includes maintaining the permissible level of Tolerance. Failure to do so can impact the functionality and integrity of the components in their applications.
2. Surface Finish
The texture and quality of the surface of the machined part refer to the surface finish. Maintaining the surface finish is important in CNC Machines because it impacts the functionality of the components.
The fine irregularities in the surface finish are measured as surface roughness. This quantitative measure is usually measured in micrometers or micro inches. Machinists use a laser scanner to measure surface roughness.
Various factors impact a component’s surface finish. These include the condition of the tool, feed rate, material properties, and the type of coolant.
Surface finish measures the quality and precision of the CNC machine itself. High-quality parts demand a smooth finish. The fewer the surface irregularities, the better the product finish.
3. Assembly and Fit
To ensure the machine parts are accurately manufactured, they must perfectly fit and assemble in the production lines. Both assembly and fit are parameters of dimensional accuracy, which is a critical parameter of Quality Control.
Adequate synchronization between the products is necessary to ensure that the parts are functionally accurate. Perfect component fitting is also important to ensure a smooth assembly line.
4. Strength and Hardness of the Material
Although most machinists do pay much attention to this factor, the strength and hardness of the material are very important to consider. The strength and hardness of a material are unique to each application. Some applications require stronger materials, while some do not. Other factors, such as the selection of raw materials and the type of machining process, depend on the strength of the material.
For example, if you want to make an object that has to be placed in harsh environmental conditions, then it has to be strong. A weak object would not be able to withstand harsh environmental conditions. It might wear easily and break. For this purpose, you need a strong material.
This is the main reason why inspection of the material is an important aspect of the quality control process.
5. Geometric Tolerance
The geometric patterns of CNC machine parts are an important aspect. Various geometric shapes include round, flattened, or straight. Applying Tolerance to such geometric shapes is known as geometric Tolerance.
Getting the geometric tolerance right is important because it ensures that the part fits and functions properly. It is not just about getting the measurements right but about conforming to the specified geometric shapes.
You need a CMM and a coordinate measuring machine to measure geometric Tolerance. These machines assess the accuracy and precision of various complicated geometric shapes.
6. Tool Quality
The cutting tool’s quality is important to ensure that the manufactured components have precise and accurate measurements. A worn-out tool will not be able to produce good-quality components.
Maintenance of tools is very important. Make sure to inspect them regularly and replace them when they wear out.
What Techniques and Tools Are Essential for Quality Control in Machining?
To ensure that the manufactured components meet the desired geometrical specifications and standards, you need tools and techniques. Each tool measures a specific measurement. Let’s examine various tools and techniques you can use during quality Control and assurance processes.
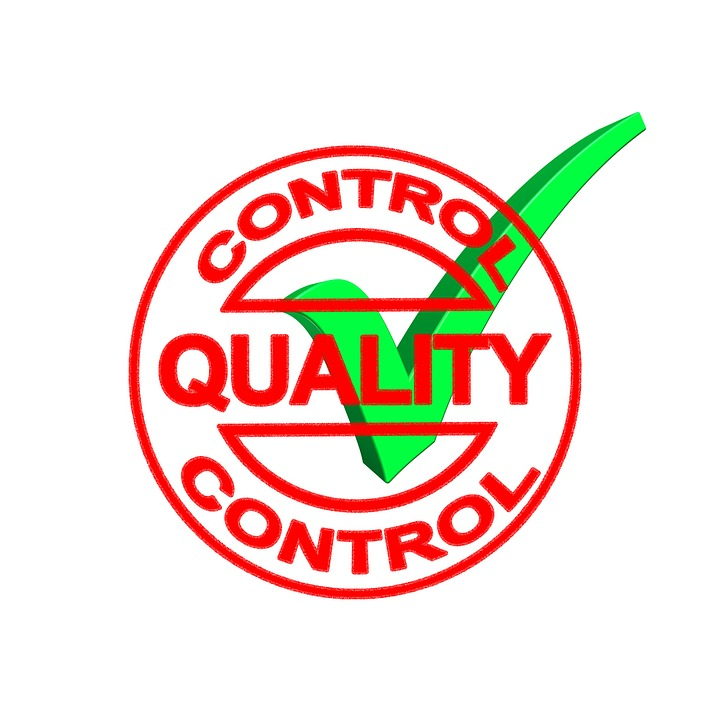
1. Testing the Surface Roughness
As part of the quality control process, checking the surface roughness of the machined parts is an important step. For this process, machinists use two types of tools, which are as follows:
1.1 Profilometer
Machinists use a profilometer to inspect a component’s surface roughness. It measures the very small variations in the component’s height. For measurement, it uses a diamond stylus that moves on the surface of the object. The measurement of surface finish is a parameter that inspects the functionality and appearance of a particular object.
1.2 Optical Comparators
The workings of optical comparators are very interesting. They magnify the surface of the object, making it easy for the machinist to inspect the surface of the part. They can easily identify any surface imperfections or defects. Defects related to the durability of the parts can easily be detected through optical comparators.
2. Hardness Testers
You must perform hardness tests to know whether a part suits a particular application. The following tools are used for this purpose:
2.1 Rockwell Hardness Tester
This method is applied to metals. It uses different depth methods to assess a material’s hardness. It consists of a Rockwell hardness testing machine, which consists of different components such as an indenter, anvil, and measuring transducer.
3. Testing the Surface Roughness
As part of the quality control process, checking the surface roughness of the machined parts is an important step. For this process, machinists use two types of tools, which are as follows:
3.1 Profilometer
Machinists use a profilometer to inspect a component’s surface roughness. It measures the very small variations in the component’s height. For measurement, it uses a diamond stylus that moves on the surface of the object. The measurement of surface finish is a parameter that inspects the functionality and appearance of a particular object.
3.2 Optical Comparators
The workings of optical comparators are very interesting. They magnify the surface of the object, making it easy for the machinist to inspect the surface of the part. They can easily identify any surface imperfections or defects. Defects related to the durability of the parts can easily be detected through optical comparators.
4. Hardness Testers
You must perform hardness tests to know whether a part suits a particular application. The following tools are used for this purpose:
4.1 Rockwell Hardness Tester
This method is applied to metals. It uses different depth methods to assess a material’s hardness. It consists of a Rockwell hardness testing machine, which consists of different components such as an indenter, anvil, and measuring transducer.
It measures the penetration depth under a large load compared to a minor load.
4.2 Brinell Hardness Tester
A Brinell Hardness tester is used to inspect soft materials. Other than being able to inspect softer materials, it also has a wider indenter. The indenter presses onto the material under a specified load.
After the pressing, the diameter of the leftover indentation is measured. This gives an idea of the material’s hardness.
5. The NDT i.e. Non-Destructive Methods
As the name indicates, nondestructive testing methods include testing techniques that do not alter or change the component or material. The following two types are the most widely used techniques in CNC Machining operations:
5.1 Ultrasonic Testing
Ultrasonic testing uses ultrasound or sound waves to check for internal flaws in the material. This method ensures the integrity of the machined parts. It is helpful because it detects damages that are not visible to the external eye.
5.2 Magnetic Particle Inspection and X-Ray
X-ray and magnetic particle inspection techniques are used to examine the internal structure of the components. X-rays use penetrating rays, and magnetic particle inspection is ideal for detecting flaws in ferromagnetic materials.
6. Tools for the Measurement of Dimensions
Since the start of this blog, much stress has been placed on measurement accuracy. Precise measurements are at the center of CNC machine operations. Machinists use the following tools to ensure that the manufactured components align with the standard measurements.
6.1 CMM (Coordinate Measuring Machine)
CMM machines are used to measure objects with complex geometric patterns. The basic purpose of using a CMM is to ensure that the object has specified geometric measurements. The machine comes in contact with the object through touch or scan and takes the measurements. These measurements are in the form of data points. Later, a map of the components’ dimensions and geometries is created using these data points.
6.2 Thread Gauges and Gauge Blocks
Thread gauges are the measuring tools for objects with threaded parts. They measure their accuracy.
Gauge blocks, on the other hand, are used to create standardized measurements. They are also known as Johannsson gauges.
6.3 Calipers and Micrometers
These are high-precision instruments. They measure the external and internal dimensions. A caliper measures the thickness, and a gauge measures the diameter. These two instruments are indispensable for checking the conformity of the tools’ measurements with the standards.
7. Monitoring the Condition of the Tools
As stated before, tool maintenance is very important in the CNC machine. It is also an important step in the quality control process.
7.1 Automated Monitoring Systems
Automated monitoring systems are integrated into CNC machines. While the CNC machining operation is running, these systems track the performance of the cutting tool. In this way, the machinists get an idea of the tool condition, which helps in the efficient running of CNC Machine operations.
7.2 Wear Measurement Devices
Wear measurement devices estimate when a tool needs replacement and how much it has worn out. They accurately gauge tool wear. Using these tools helps machinists know when to replace tools so that they do not impact the efficiency of CNC machine operations.
8. Tools for Visual Inspection
Although simple enough, it is a very important part of the quality control process in CNC machining. The following two tools are used for visual inspection:
8.1 Borescopes
Borescopes allow you to have a bird’ s-eye view of invisible material properties to the human eye. Just insert the tool through a small opening to get an idea of the internal structure. Then, you can easily inspect any flaws if they exist.
8.2 Magnifying Glasses
It measures the penetration depth under a large load compared to a minor load.
8.3 Brinell Hardness Tester
A Brinell Hardness tester is used to inspect soft materials. Other than being able to inspect softer materials, it also has a wider indenter. The indenter presses onto the material under a specified load.
After the pressing, the diameter of the leftover indentation is measured. This gives an idea of the material’s hardness.
9. The NDT i.e. Non-Destructive Methods
As the name indicates, nondestructive testing methods include testing techniques that do not alter or change the component or material. The following two types are the most widely used techniques in CNC Machining operations:
9.1 Ultrasonic Testing
Ultrasonic testing uses ultrasound or sound waves to check for internal flaws in the material. This method ensures the integrity of the machined parts. It is helpful because it detects damages that are not visible to the external eye.
9.2 Magnetic Particle Inspection and X-Ray
X-ray and magnetic particle inspection techniques are used to examine the internal structure of the components. X-rays use penetrating rays, and magnetic particle inspection is ideal for detecting flaws in ferromagnetic materials.
10. Tools for the Measurement of Dimensions
Since the start of this blog, much stress has been placed on measurement accuracy. Precise measurements are at the center of CNC machine operations. Machinists use the following tools to ensure that the manufactured components align with the standard measurements.
10.1 CMM (Coordinate Measuring Machine)
CMM machines are used to measure objects with complex geometric patterns. The basic purpose of using a CMM is to ensure that the object has specified geometric measurements. The machine comes in contact with the object through touch or scan and takes the measurements. These measurements are in the form of data points. Later, a map of the components’ dimensions and geometries is created using these data points.
10.2 Thread Gauges and Gauge Blocks
Thread gauges are the measuring tools for objects with threaded parts. They measure their accuracy.
Gauge blocks, on the other hand, are used to create standardized measurements. They are also known as Johannsson gauges.
10.3 Calipers and Micrometers
These are high-precision instruments. They measure the external and internal dimensions. A caliper measures the thickness, and a gauge measures the diameter. These two instruments are indispensable for checking the conformity of the tools’ measurements with the standards.
11. Monitoring the Condition of the Tools
As stated before, tool maintenance is very important in the CNC machine. It is also an important step in the quality control process.
11.1 Automated Monitoring Systems
Automated monitoring systems are integrated into CNC machines. While the CNC machining operation is running, these systems track the performance of the cutting tool. In this way, the machinists get an idea of the tool condition, which helps in the efficient running of CNC Machine operations.
11.2 Wear Measurement Devices
Wear measurement devices estimate when a tool needs replacement and how much it has worn out. They accurately gauge tool wear. Using these tools helps machinists know when to replace tools so that they do not impact the efficiency of CNC machine operations.
12. Tools for Visual Inspection
Although simple enough, it is a very important part of the quality control process in CNC machining. The following two tools are used for visual inspection:
12.1 Borescopes
Borescopes allow you to have a bird’ s-eye view of invisible material properties to the human eye. Just insert the tool through a small opening to get an idea of the internal structure. Then, you can easily inspect any flaws if they exist.
12.2 Magnifying Glasses
Magnifying glasses are used for detailed visual inspection of the outer surface of the m=components. They help you analyze the external surface through the human eye. They magnify the external features so that you can make sure the parts do not deviate from the quality standards.
What are all machining quality testing and inspection stages?
1. Inspection of Raw Materials
One of the initial inspections in the CNC machine operations is the inspection of raw materials. This step includes inspecting the following:
- The packaging of raw materials
- Their measurements
- Their surface finishes
Good-quality raw materials will have intact packaging, a smooth surface, and, most importantly, accurate measurements.
2. Tool Inspection
After ensuring that the raw materials meet the quality standards, the next step is tool inspection. You have to ensure that the tool placement and the workpiece placement are intact, that the tool is well maintained, and that the tool has good spinning and linear axis movement ability.
3.First Article Inspection (FAI)
Exactly after modification through CNC machining operations, a product goes through the first article inspection (FAI). The FAI inspects the product for several standards and monitors whether it passes the ISO9001 standards.
Other assessments include making sure that the product is accurate and precise:
- Dimensional characteristics
- Manufacturing specifications and
- Quality requirements.
Technological advancement has revolutionized the FAI process. Previously, it required much paperwork to complete. Net Inspects software has now replaced the hefty paperwork.
4. In Process Inspection
As the production process continues, the in-process inspection ensures that the product does not contain any manufacturing defects and meets all the measurement standards.
5. Final Inspection
Of course, the final inspection occurs after complete product manufacturing. It checks if the product conforms to all the dimensional and quality parameters. Precise manufacturing is important to ensure that parts fit together accurately and form a smooth assembly line.
6. Assembly and Fit-Up Inspection
This is the step during which the parts are synchronized. It occurs after ensuring that all the manufactured parts are up to standard quality and checking them for geometrical tolerances.
7. Statistical Process Control
Statistical process control methods effectively manage CNC Machine operations. These methods ensure that the manufactured products have precise and accurate measurements. Certain software can make the process easy. This software provides efficient performance tracking systems and advanced analysis.4.0 SPC software is an example of one such system.
How Crucial is Personnel Training in Machining Quality Control?
Be it any process other than CNC machining, you must always pay attention to the importance of skilled personnel. Of course, if the machinists do not know their job, even the perfect machinery cannot do anything. CNC machinery and tools are very complicated. Therefore, only skilled labor can work on them.
Skilled labor has many advantages. They can identify any possible issues, monitor the quality control processes efficiently, and, most of all, easily adapt to any changes in the processes or tools.
It is recommended that the operating staff receive good training periodically. This keeps them updated about technological advancements and operating procedures.
Conclusion
Manufacturing error-free machining parts through CNC machine operations is a huge challenge. However, it is not impossible to achieve. You can easily accomplish this by combining skilled labor, error-free machines and tools, and effective quality control methods.
By staying aware of technological advancements in the quality control fields, using software and manual and digital control methods, you can manufacture components with precise and accurate measurements and designs. This ensures a smooth fit of parts together.
This is all possible through effective and efficient quality control and quality assurance methods.