Plastic injection molding is a complex and expensive process. Yet the extensive use of plastic products in almost every field has made its implementation vital. From automotive, to household and medical industry the use of plastics is inevitable. Of course, this process uses injection molding technique. But HOW?
Also, there are variety of thermoplastics that are used in this process. Which thermoplastic will be used for which purpose depends upon the desired product. This blog begins with the explanation of the plastic injection molding process. Afterwards it explains the top 10 plastic injection molding materials in detail.
The Injection Molding Process
In simple words it is just a process to make plastic parts and obtain molded products. It consists of simple steps. First of all, the relevant plastic polymer is heated and converted to molten form using heat. Once melted the plastic poured into a set mold.
In the later steps the plastic in the mold is allowed to set. It is then cooled down until it solidifies.
The injection molding process is suitable for the manufacturing of products of complex shapes. It is a process used at industrial level for mass production.
The implementation of this process consists of simple steps which are described below:
1.Selection of the Appropriate Mold
Before the actual process begins selection of the right mold is very important. The selection of the right mold depends upon the material selection of thermoplastic you are using as well. It is therefore advisable to use 3d printing. With the help of 3d printing you can design a prototype of the mold cavity and see if it fits well or not.
2.Selection of the Right Thermoplastic
Selection of the right thermoplastic depends upon the properties of the product you are looking for. Different thermoplastics have different properties. You need to shortlist the properties such as maximum and minimum temperature range, water resistant, light weight etc.
3.Melting the Thermoplastics
First of all, raw plastic resins are added into the barrel with the help of a hopper. Then heat is provided. This heat can be generated either through electricity or hydraulics. Once heated the two plastic resin resins get converted to liquid polymer form.
After conversion to molten material the liquid polymers are send to mold box. Injection of the plastics into the mold causes the two halves of the mold box to close. At the same time pressure is applied resulting from clamping.
4.Holding Time
The liquid is then kept into the mold for a particular period of time until it sets. The pressure on the mold is maintained. The duration and amount of pressure depends upon the type of thermoplastic being used. This process is known as holding time. It is important to give the liquid proper shape inside the mold.
5.Cooling Time
After the completion of the holding time the pressure is released and the mold is opened. The resulting product is then allowed to cool down. This process is known as cooling time. This is the last step before ejection of the product in the product line. The duration of the cooling time ranges from a few milliseconds to minutes.
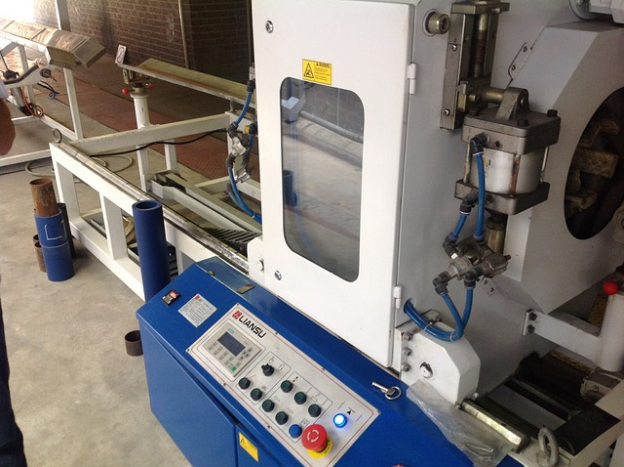
Nylon Polyamide (PA)
Nylon is made from petroleum. The melting and conversion of petroleum into fibers, films or shapes make nylon. Also known by the name of its family nylon is also called polyamide (PA). Polyamide is a family of synthetic polymers.
Several types of nylon are used in the injection molding process. The most common types are:
- Nylon 6
- Nylon6/6
- Nylon 66
Properties
- Nylon has the following properties:
- It offers high abrasion resistance
- It is tough and offers strong mechanical properties.
- Offers good fatigue resistance
- It has high heat resistance
- It has noise dampening properties
- Although not flame resistant but offers versions that resist flame
- It does not resist ultraviolent rays of the sun. However, with the addition of UV stabilizers it can be made suitable for use in outdoor applications.
Applications
Because of toughness nylon injection molding has a lot of commercial applications such as:
Automotive Industry
Production of mechanical parts such as gears caster wheels, bears and bushings. It means that it has uses in the automotive industry. It is used in the making of wear pads, guide wheels and quick release buckles.
Material limitations
Along with all the good properties and toughness Nylon has one major drawback. It is that it is not water resistant. This is the major reason that nylon use is not recommended in marine applications.
Acrylonitrile Butadiene Styrene (ABS)
ABS plastic is a resin. ABS is opaque in nature. It is an engineering thermoplastic. The polymerization of styrene and acrylonitrile in the presence of polybutadiene makes ABS. The mixing proportions of the materials can be different. Let’s have a look at its properties and applications.
Properties
The most important property of ABS is that it has good dimensional stability. Having dimensional stability means that it offers good resistance to scratches. It is also non-breakable.
- It is an insulator.
- Light weight.
- It offers good resistance to flame.
- A unique property is that it is easy to mold.
ABS is not resistant to UV rays or sunlight. Therefore, it is not a good material for outdoor applications.
Applications
Because ABS is a good molding material it has several applications in the electronics industry. It is used in the making of
- Keyboard keys
- Mobile adapters
- sports equipment etc.
Acrylic
Acrylic is also known by the name of “Proxiglass”. There are several reasons behind this name. It is because of the transparent nature of the material. Acrylic is a transparent, plastic material. It is because of its transparent nature that is used as a cheap alternative to glass.
Rohm and Haas company are the founders of acrylic. Although its invention took place in 1928. Rohm and Haas company introduced it into the market five years later. It is the most transparent high impact resistance forms of plastic available in the market. The chemical composition of acrylic is Polymethyl Meth Acrylate.
Properties
Acrylic material offers high resistance to fluctuations in temperature.
- Offers high level consistent quality of optical clarity.
- As compared to glass it is lighter in weight.
- It is an ideal material for precision machining.
- Offers high chemical resistance.
Its impact resistance as compared to glass is also high.
Applications
Medical equipment
High chemical resistance to chemicals makes acrylic suitable for the manufacturing of medical manifolds. This is a major application of acrylic in the medical industry.
Optical Devices
Because of the optical clarity and transparency, it is highly suitable for use in the manufacturing sector of lenses and optical devices.
CNC Machining
Acrylic is the most recommended material for CNC Machining precision components. It is because of shock and high impact resistance.
Polycarbonate (PC)
Polycarbonate (PC) is a high-grade engineering thermoplastic. It is a clear injection molding resin. It is popular for its versatile applications and uses. Although it is expensive material yet its price is balanced by its versatility to use.
Properties
- It is a tough material
- Offers high resistance to abrasion and friction
- It has extremely high melting point of 155’C.
- Offers high insulation to electricity
- It is transparent in nature
Applications
Since it is transparent and tough it is the most suitable material for bullet proof glass.
It is used in the manufacturing of electrical connectors and insulators
Diffusers and light pipes for light emitting diodes (LED’s) also use polycarbonates.
It has amazing optical properties and offers great durability.
It has some material limitations as well. It is its non-suitability for use in food containers.
Polyethylene (PE)
Polyethylene is the among the most common injection molding materials. The selection of this polymer is done on the basis of its density. High density polyethylene (HDPE), medium density polyethylene (MDPE) and Low-density polyethylene (LDPE)are all the categories of polyethylene on the basis of its density.
Properties
Low density polyethylene has several unique properties. Even at low temperature it remains flexible. It takes a lot of pressure before it breaks. It has high ratio of strength to density. Moat of all it is odorless, light and sterile.
Medium density polyethylene offers high chemical resistance. It also has high impact resistance. The strength value of MDPE lies between LDPE and HDPE. Also, it is susceptible to factors such as UV rays and solvents.
High density polyethylene is:
- It is light weight
- Offers poor resistance to UV light.
- It shows poor temperature resistance.
- It offers crystalline properties while remaining rigid.
- It has high value of tensile strength.
A major disadvantage of this thermoplastic is that it shrinks inside the mold after cooling down. This can cause dimensional stability and problems with part tolerances. Experts can reduce this damage by predicting beforehand the amount of shrinkage that might occur after cooling down.
Applications
This is the most common type of plastic used in the world. It has wide range of applications such as:
- Manufacturing of toys
- Plastic bottles
- automotive parts and
- housewares.
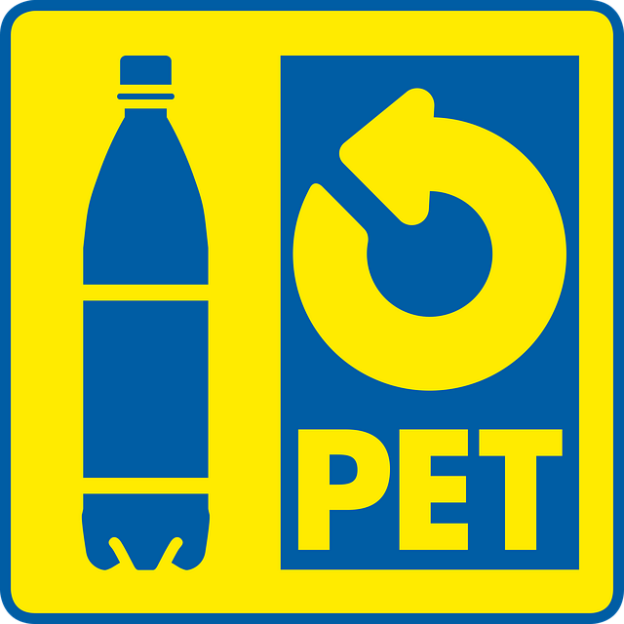
Polyoxymethylene (POM)
Polyoxymethylene is also known as polyacetal. Because of the fact that this plastic is used in the large-scale manufacturing of high-performance engineering components it is also known as engineering plastic. These plastics offer a large number of variable properties which are as follows.
Properties
- They offer a low linear coefficient value of thermal expansion.
- They maintain their chemical properties to high and low temperatures throughout. The maximum temperature is -40’c to which they maintain their mechanical properties.
- They do not absorb water.
- They are permeable.
- Polyacetals offer good dimensional stability.
- These are glossy and hard mold making materials.
- To most of the chemicals, solvents and fuels they offer high resistance that too at room temperature.
Applications
The applications of these plastics are widespread. They are used in the manufacturing of automotive parts such as gears, conveyor belts, seat belts, and bearings.
In the housing industry they are used in the making of creep resistant housings, exterior panels, lock systems and wear resistance surfaces.
Polypropylene (PP)
Polypropylene (PP) a linear hydrocarbon is amongst the most versatile polymers available. It is because it has characteristics of both plastic and fibers.
Properties of Polypropylene (PP) injection molding:
- It has good heat resistance.
- Offers excellent chemical resistance
- Tough and translucent
- they have slippery and tactile surface textures.
You might be thinking that the mechanical properties of polypropylene are similar to that of polyethylene. However, this is not the case. There are some clear differences between the two. The major difference is between the melting point. The melting point of polypropylene is 1600’C and that of ethylene is 1000’C.
Applications
Polypropylene is used in a variety on injection molding applications. These applications spread around variety of industries.
In the automotive industry they are used for the manufacturing of battery casings, bumpers, interiors etc.
They are used for the packaging of goods and food items. It is because of their corrosion resistance to chemicals.
They have variety of medical applications as well. Pill containers, specimen bottles and syringes etc. are all made of polypropylene.
They are also used in the making of toys, bleaches, first aid products etc.
Polystyrene (PS)
Considering injection molding resins polystyrene is of two types:
High Impact Polystyrene (HIPS)
General Purpose Polystyrene (GPPS)
The main difference between these two types is that the former is opaque and the latter is transparent in nature. The dimensional stability of GPPS is also less than HIPS.
Properties
The material properties of Polystyrene are as follows:
- It is tough and durable.
- Resists moisture and growth of bacteria
- It offers good chemical resistance to acids and bases.
- It is flammable
Applications
- Polystyrene injection molding has several applications in the medical, electronic and optical industries.
- Gamma radiation used in the sterilization of medical devices also uses polystyrene.
- GPPS after injection molding is used in the manufacturing process of toys, containers, and trays.
Thermoplastic Elastomer (TPE)
Thermoplastic elastomer is a combination of plastic and rubber. A unique property of this material is that it once stretched it can come back to its prior position. The best characteristic is that it is recyclable.
Properties
It is easy to mold especially when comparing to silicone rubber.
It is expensive as compared low cost to other plastic injection molding materials.
At high temperature it loses its properties to other methods of rubber such as elasticity. In fact, it may deform.
Applications
It has several applications in:
- Medical devices
- foot wear
- Automotive manufacturing sector,
- Pet products etc.
Thermoplastic Polyurethane (TPU)
What makes thermoplastic polyurethane is its unique feature of having the characteristics of both rubber and plastic materials.
Properties of thermoplastic Polyurethane (TPU) Injection Molding
It is strong and offers great tensile strength
It offers rubber like elasticity.
Offers good load bearing capabilities
TPU injection mold has the ability to withstand ozone.
Applications
Thermoplastic polyurethane replaces polyvinyl chloride in medical industry. It is because PVC can cause allergic reactions in patients. TPU injection molding has several applications such as:
- sports goods
- footwear
- protective wire, cable sheaths gaskets and other materials.
CONCLUSION
Different thermoplastics have different properties. They differ in their thermal, physical and mechanical properties. They offer different resistances to different aspects such as temperature, chemical, shock etc. The selection of the right thermoplastic is crucial to this process.
Also, the perfect shape of the mold is mandatory. Other factors that need attention are the right application of pressure and maintenance of temperature. Not just the right resources but right expertise is critical to the success of plastic injection molding process.