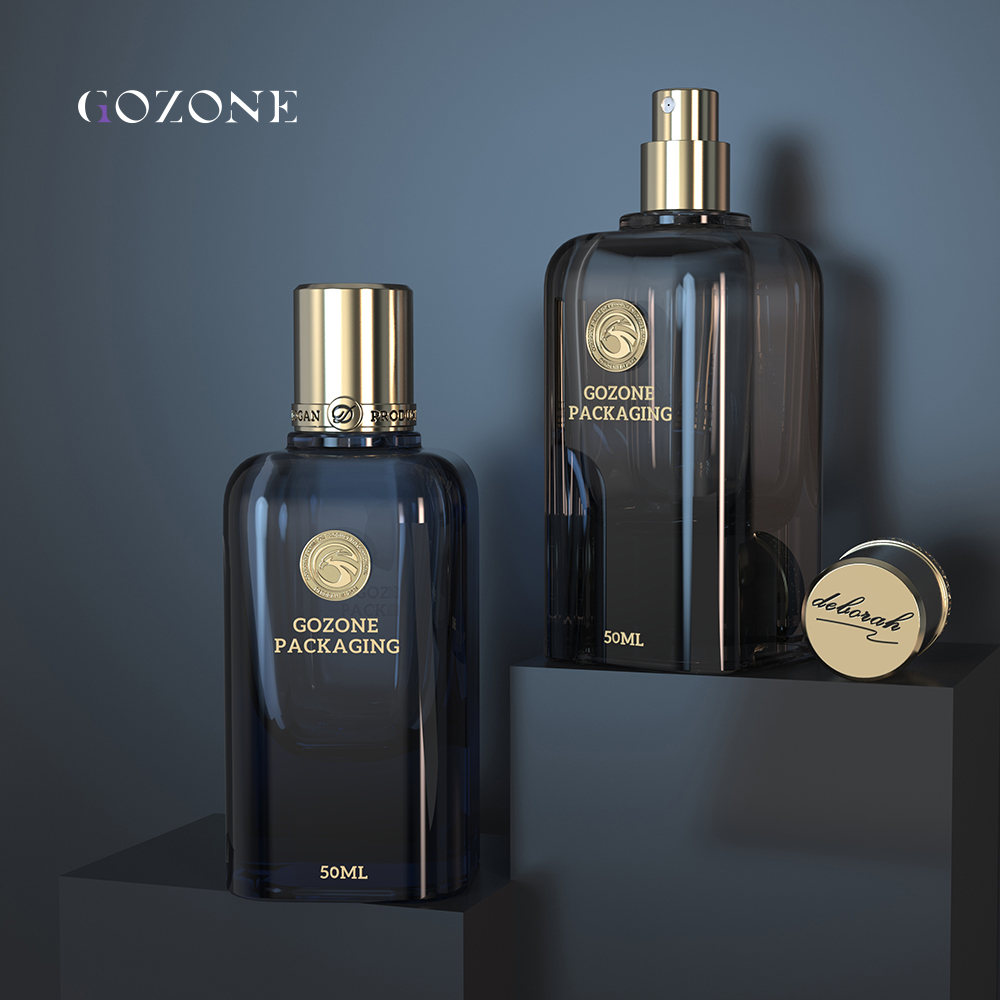
Behind each captivating fragrance lies a meticulous process that upholds the highest standards of craftsmanship and functionality. In this blog post, we delve into the intricate art of perfume bottle quality control, where meticulous attention to detail ensures uncompromising excellence.
Discover the critical role of quality control in safeguarding a brand’s reputation and delivering an unmatched consumer experience. Join us as we explore essential aspects such as visual aesthetics, material compatibility, manufacturing processes, and cutting-edge technology, all integral to the creation of flawless perfume bottles.
The significance of quality control
erfume bottles are more than just containers for fragrances. They are expressions of the brand’s vision and values, as well as sources of delight and satisfaction for customers.
Every bottle has to follow high standards for design, materials and function, as well as meet safety regulations. This ensures the quality of the perfume bottles and the satisfaction of the customers.
A quality perfume bottle enhances the fragrance’s appeal and creates a lasting impression on the customer’s senses. Quality control is not an optional step, but a core element of the perfume industry.

Aesthetic Appeal and Visual Inspections
The perfume inside the bottle is not the only thing that matters. The bottle’s design also has to be perfect. Quality control ensures that every bottle looks flawless and attractive.The bottle’s design is part of the perfume’s charm.
The design team makes sure that the shape, color, and materials of the bottle are flawless and stylish. The bottle’s design is carefully inspected and refined to create a beautiful and elegant impression.
The design of the bottle also reflects the brand image and appeals to the target market. Aesthetic evaluation is essential to create a beautiful and enticing product.
Assessing Aesthetic Appea
Ensuring functional excellence is of utmost importance in perfume bottle quality control. Beyond the allure of visual aesthetics, bottles must deliver a seamless user experience. Closures, caps, and sprayers undergo rigorous evaluations to guarantee durability, ease of use, and optimal functionality.
Thorough testing methods are employed to assess their performance, including leak resistance, proper sealing, reliable spray dispersion, as well as weight and thickness checks.
By meticulously scrutinizing these functional aspects, quality control ensures that the bottle not only exudes beauty but also delivers a flawless and user-friendly experience, enhancing customer satisfaction and the overall usability of the fragrance product.
Material Selection and Compatibility
The meticulous selection of materials and their compatibility is a crucial aspect of perfume bottle quality control. Careful consideration is given to choosing materials that align with the brand’s vision while preserving the fragrance’s integrity.
Compatibility tests are conducted to ensure the selected materials do not react with the perfume, ensuring its scent and quality remain unaltered over time. Assessments encompass factors such as resistance to chemical reactions, degradation, and leakage.
Through meticulous material selection and compatibility testing, quality control guarantees the perfume bottle’s reliability, longevity, and ability to preserve the fragrance’s essence, delivering an enchanting experience to consumers.

Manufacturing processes and quality assurance
Perfume bottle production process
The production process of perfume bottles involves a series of meticulous steps to create exquisite vessels that complement the fragrance they hold.
It begins with the design phase, where skilled designers translate concepts into precise technical drawings.
Next, careful material selection is made, considering factors such as glass clarity, plastic durability, or metal elegance.
Manufacturing techniques like glass blowing, plastic injection molding, or metal forming are then employed to shape the bottles with utmost precision. S
urface treatments such as polishing, painting, or etching are applied to enhance the aesthetics.
Throughout the process, stringent quality control checks ensure visual appeal, functional integrity, and compatibility with the fragrance.
Finally, the bottles are meticulously packaged, ready to be distributed and carry the essence of captivating scents to discerning customers worldwide.
Quality control measures at different stages of production
Quality control measures are diligently integrated at various stages of perfume bottle production to ensure uncompromising excellence. During material selection, stringent assessments verify materials for fragrance compatibility and durability.
Throughout manufacturing, automated systems, machine inspections, and skilled operators monitor processes, rectifying defects and inconsistencies. Surface treatments are carefully examined for flawless finishes, while functional elements like closures and sprayers undergo thorough testing.
Finally, comprehensive visual inspections confirm that each bottle meets the highest standards of craftsmanship and aesthetics. These meticulous quality control measures guarantee that the finished perfume bottles embody quality and elegance, ready to embrace the most enchanting fragrances.
Conclude
Perfume bottle quality control involves a collaborative effort, blending precision and meticulous attention to detail. Experts from various fields, including designers, engineers, manufacturers, and quality assurance teams, ensure excellence throughout the process.
From material selection to final presentation, nothing falls short of perfection. The unwavering focus on functionality, aesthetics, and craftsmanship elevates the fragrance industry, creating captivating sensory experiences worldwide. Each perfume bottle becomes a work of art, preserving the allure of fragrance for generations to come.