In the realm of packaging, glass bottle testing holds critical importance. Ensuring consumer safety and product quality, tests have been refined over time. Among them, the Helium Leak Test, Top Load Test, and Squeeze Test stand out, offering insights unparalleled in assessing bottle integrity.
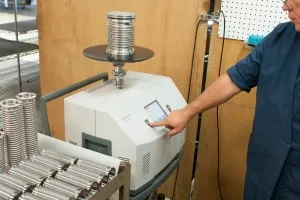
Source:compuvacind.com
Helium Leak Testing: Guaranteeing Glass Bottle Safety
When it comes to the quality assurance of glass bottles, safeguarding against leaks is crucial. The Helium Leak Test is an advanced technique designed to meticulously assess glass bottle integrity, making certain its contents are well-protected.
Role and Purpose
Ensuring packaging safety and content purity, the Helium Leak Test stands as a beacon in advanced testing techniques.
By leveraging helium’s unique properties, it offers manufacturers a precise method to detect even the smallest imperfections or breaches in the seal, underscoring its importance in the realm of quality assurance.
Testing Procedure
The Helium Leak Test operates based on helium’s tiny atomic size, allowing it to pass through minuscule gaps. For the test, bottles are filled with helium and then sealed.
They’re placed in a vacuumed chamber where any escaping helium—due to pressure differences—is detected by sensitive detectors. This method pinpoints leaks, verifying glass bottle integrity and ensuring packaging safety.
Significance
For industries prioritizing the pristine condition of their products, from perfume bottle resilience to beverage freshness, the Helium Leak Test is indispensable.
It reassures both manufacturers and consumers that every bottle meets the highest standards of quality assurance, ensuring the contents remain uncontaminated and true to their original form.
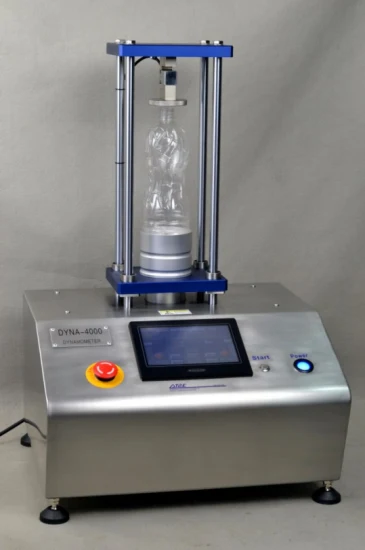
Source:Made-in-China.com
Top Load Test: Assessing Glass Bottle Strength
The strength of glass bottles is vital, especially when they’re stacked or subjected to external forces during transportation and storage. The Top Load Test is an essential procedure, focusing on evaluating the vertical force a bottle can endure without deforming.
Role and Purpose
The Top Load Test’s primary objective is to simulate the vertical stresses a bottle might encounter, such as stacking pressures or downward forces during handling.
This test provides insights into the bottle’s structural design and material strength, ensuring it doesn’t buckle under weight, thus maintaining packaging safety and glass bottle integrity.
Testing Procedure
In a Top Load Test, a downward force is applied to the top of the bottle until it either deforms or breaks. The amount of force it can withstand before deformation indicates its vertical load strength. Modern machines monitor and record the applied force, offering precise data to manufacturers.
Significance
A bottle’s ability to resist vertical force is paramount in ensuring its contents remain protected, especially during shipping and warehousing. The Top Load Test offers an assurance of the bottle’s strength and durability, reinforcing confidence in its quality assurance and design.
Squeeze Test: Evaluating Glass Bottle Flexibility
Glass bottles, while often perceived as rigid, may need a certain degree of flexibility, especially for specific applications like perfumes. The Squeeze Test is designed to measure this flexibility, ensuring the bottle’s design meets both functional and quality assurance requirements.
Role and Purpose
The primary aim of the Squeeze Test is to determine how a bottle responds to compressive forces from the outside. It’s essential for scenarios where consumers might press the bottle for product dispensation, emphasizing the importance of perfume bottle resilience. The test gives insights into the bottle’s material and design, ensuring it doesn’t crack or break under pressure.
Testing Procedure
During the Squeeze Test, controlled compressive forces are applied to the bottle from multiple angles. Instruments monitor the bottle’s response to these forces, capturing data on its deformation and the point at which it might fail. This provides valuable data on the bottle’s design and material choice.
Significance
In industries where tactile interaction with the bottle is common, like in fragrances or certain beverages, a bottle’s flexibility becomes a key factor in user experience. The Squeeze Test ensures that these bottles not only retain their glass bottle integrity but also offer the desired tactile feedback, contributing to product success.
In Conclusion
From understanding micro leaks to gauging structural resilience and assessing tactile flexibility, this series has provided a comprehensive look into glass bottle testing. It’s a testament to the dedication of manufacturers to quality assurance and the safety of consumers.
As we conclude, we take a moment to appreciate the nuanced complexities of packaging safety and the standards that keep us assured of every bottle’s reliability.