Have you ever wondered what gives extra shine to cutlery and door knobs? Where does the luster of the automotive parts come from? This versatile metal forms a shiny coating on metals and plastics.
That metal is chrome.
Chrome plating is a widely used process because it gives materials a desirable shine. It not only makes the materials look more luxurious but also increases their durability. Although very useful, the process is not that simple in terms of manufacturing.
This is probably why chrome plating is performed in large-scale manufacturing industries. However, sometimes, for several reasons, you need to remove the chrome plating from the metal.
You should change the color of the titanium underneath. In some cases, the chrome layer has lost its shine because of wear and tear, and you want to remove it. If you don’t know how to remove the chrome plating from metal parts, this blog is for you.
This blog provides a detailed explanation of the complete chrome plating process and how to remove it. From processes to applications, it covers every detail about chrome plating and its removal.
Understanding Chrome Plating
1.Composition of Chrome Plating
Chrome plating is the process of depositing a layer of chrome on the surface of a metal. The electroplating technique is used for chrome plating. The metals on which chrome plating is done are usually aluminum, brass, nickel, or steel.
The basic purpose behind chrome plating is to increase the shine, finish, and appearance of the materials. Not only does it increase the shine, but it also makes them more resistant to corrosion. In fact, it increases their durability.
2.Reasons for Removal
2.1Damaged Metal Underneath
Sometimes, the metal underneath could be of outstanding better quality, and as a result, it becomes damaged. To repair it, the chrome plating above it must be stripped off. It is therefore important to use good quality metal for chrome plating. In case of poor quality of the metal underneath the chrome plating layer on surface will also be tarnished.
2.2Aesthetic Changes
Aesthetic are important for all materials and parts. This is especially true for automotive parts such as alloy rims. You need to change the aesthetics of a material. For this purpose, you first need to remove the chrome plating on it if you want to plate a new metal with a different color and aesthetics.
2.3Re-Plating
Chrome is amongst the highly resistant and durable metals.Sometimes, the chrome plating layer gets scratched and wears out because of prolonged use. As a result, the material loses its corrosion-resistant properties and shine. In such cases, you need to remove the old chrome plating layer. Re-plating can help get a new one.
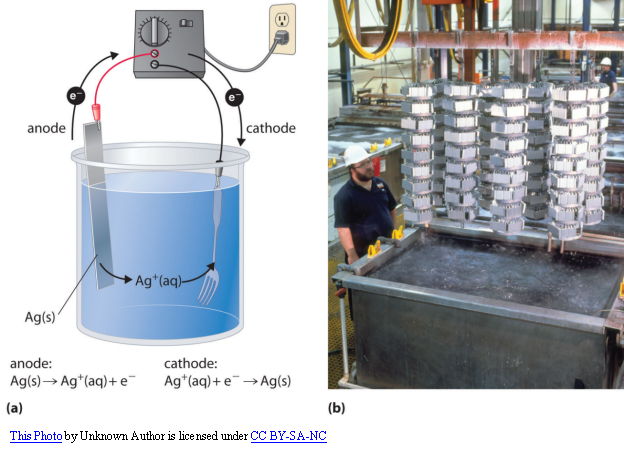
Safety Precautions
1.Health and Safety Risks
You are exposed to various health and safety risks while conducting the removal of chrome plating process. The chemicals used in the process are toxic and hazardous. They have several potential health risks for the people involved in the process.
Most of the time, the metals from which the plating is to be removed are complex or have sharp, pointed edges. It is, therefore, very dangerous to handle such objects.
High temperature and use of electric current are other potential risks to health and safety.
2.Protective Gear
The use of protective gear and equipment can help prevent health and safety risks and protect against hazardous and toxic chemicals.
Workers should wear gloves, masks, and goggles during the process. These protect them against toxic chemicals, sharp edges, and hazardous gasses. Wearing appropriate clothing during the process can also help protect against health and safety risks.
3.Safe Work Environment
It would help if you had a safe work environment to carry out the removal of chrome plating. Ensure that the area where you carry out the process is well-ventilated. This helps in the ventilation of hazardous gasses. These gases can sometimes be flammable as well, such as hydrogen gas.
Certain techniques, such as chemical stripping, produce residuals or waste materials in the form of precipitates. In such cases, ensure that proper disposal of waste materials is arranged.
Chemical Stripping Methods
1.Introduction to Chemical Stripping
The Chemical stripping process involves using chemicals to remove chrome plating from the surface of metals. It is a simple step-by-step process which is as follows:
- Take a chemical solution and bring it in contact with the chrome surface of the metal substance. Continue this step for some time.
- Clean the metal substance with cold water.
- Dry the substrate with the help of a blow dryer.
- Repeat the steps repeatedly until the chrome plating layer is removed.
Chemical stripping of chrome plating uses three types of solutions, which are mentioned below
3.Acid-Based Solutions
Acid-based solutions use acids such as sulphuric acid and hydrochloric acid. When chrome metal is exposed to an acidic solution such as hydrochloric acid, it dissolves. The chrome reacts with HCL and forms a solution that contains the Cr (ll) ion and releases hydrogen gas.
A high quantity of HCL solution containing 30-40 percent acid is needed. The exposure of chrome plating to sulphuric acid results in the formation of a precipitate. This process is also known as wet etching.
Time is a critical factor in this process. The metal should remain in the acidic solution until the chrome plating is completely removed. If the metal remains in the solution for too long, its surface might be damaged.
Once the chrome plating wears off, wash the substrate with water and blow dry it.
4.Alkaline-Based Solutions
Similar to acids, alkaline or basic solutions can also be used to remove chrome plating from metal objects. Sodium hydroxide is a base that removes the chrome layer from the surface of the metal.
Follow the same steps of chemical stripping as with the acid-based solutions. After some time of submerging, the chrome layer will fall off from the surface of the metal.
It is important to always wear gloves during the chemical stripping process. The acid—and alkalinity-based solutions can otherwise harm the hands.
Mechanical and Physical Removal Methods
1.Thermal Decomposition
As the name implies, thermal decomposition uses heat to break down chrome. The metal object is exposed to a high temperature, i.e., 400-450 degrees Celsius. Many metals are heat-resistant and corrosion-resistant. I
t is difficult to remove chrome plating with mechanical abrasive methods. Thermal decomposition is the ideal method for such metals. This is the most common technique, especially for aerospace metallic objects.
A major advantage of this technique is that it removes chrome plating while keeping the metal’s mechanical characteristics intact.
2.Sanding
An abrasive blasting sanding uses solid silica particles or crushed glass to remove chrome from metal parts. For more significant impact, the abrasive materials are forced through a nozzle onto the surface of the metal.
Clean the metal with a soap solution before you start the sanding process. Sandpaper, sanding blocks, or power sanders are commonly used for this purpose. Sanding is a standard process for removing chrome plating from automotive wheel rims.
Always take the necessary safety precautions while implementing the sanding process. It is advisable to carry out the process in a large room with open windows. In the absence of precautionary measures, sanding can result in breathing problems.
3.Grinding
When tight tolerance and excellent surface finish are priorities, grinding is the best process to remove unwanted chrome metal from the metal surface. It uses high-precision machinery, such as angle grinders and bench grinders.
Grinding is a high-precision step-by-step process. The grinding machine has wheels. These wheels are made of abrasive materials such as aluminum. During the grinding process, the following steps take place:
- The metal (from which chrome plating has to be removed) is positioned in contact with the grinding machine.
- The wheels of the grinding machine come in contact with the metals. As the wheels run over the surface of the metal, an abrasive action takes place. This abrasive action removes the chrome plating from the metal surface.
- The process continues until the desired finish is obtained.
Grinding is a favorable process when exact dimensional specifications and precision are top priorities. However, the process produces a lot of heat and friction. Lubricants and cooling agents can prevent the dissemination of heat.
4.Blasting
Also known as abrasive blasting, this technique uses powder spray to remove chrome plating from materials. The powder spray consists of sand, aluminum, steel shots, or glass beads. It uses specialized machinery for this purpose, such as an abrasive blaster.
Sandblasting is the most common technique to remove chrome plating from automotive parts, so it is widespread to find sandblasting sprays in automotive shops.
While using the blasting technique, one has to be very careful. Protective equipment such as goggles, masks, and gloves is mandatory. Tiny particles disperse in the air during the removal of the chrome plating process, and they are dangerous to the eyes and lungs.
The blasting technique is most helpful in removing decorative chrome or hard chrome from the surface of metals.
Electrolytic Removal Methods
1.Introduction to Electrolytic Removal
Another method to remove chrome plating from metals is reverse electroplating. The chrome on the metal surface is in the form of positive ions. Reverse electroplating is a highly complicated process that requires only experts to implement.
This process results in carcinogenic and hazardous chemicals.
2.Setup and Equipment
Along with the complete electrolysis setup, reverse electroplating involves sulphuric acid, chromic acid, and direct current. A strong acidic mixture that contains acid and water in a ratio of 100 to 1 is used.
Temperatures are maintained between 120’F and 150′ F. The setup for reverse electroplating includes the following materials along with the acidic solutions:
- A source of direct current is a battery.
- The metal object from which the chrome plating is to be removed.
- A positive cathode is why this method is known as reverse electroplating: the cathode has a positive charge instead of a negative charge.
3.Step-by-Step Process
- The first step is preparing the mixture of acids containing chromic acid, sulphuric acid, and water.
- In the next step, you heat the acidic solution. The solution’s heating temperature depends upon the type of chrome plating on the metal surface.
- A negative current is then released from the DC power source.
- This current passes through the electrolytic solution to the metal object to be stripped. The metal object is connected to the positive cathode and is already submerged in the electrolytic or acidic solution.
- The electric current continues to flow unless the chrome plating is completely removed from the metal surface.
- After the removal of the chrome plating, the object is thoroughly rinsed and dried.
4.Safety Considerations
The existence of electric current increases the chances of electrocution. Also, the electrolytic solution is highly acidic. Therefore, extra care should be taken when conducting this process. It is advisable that this process take place only under the supervision of professionals.
Other Methods of Removing Chrome Plating from Metals
1.Ultrasonic removal
This technique of removing chrome plating from metals uses specialized equipment, such as ultrasonic cleaners.Ultrasonic cleaners use sound wave frequencies to remove small particles of dust, grime, or other substances from materials.
When using ultrasonic cleaners for the removal of chrome plating from metals, the process consists of the following steps:
- The metal surface comes in contact with the ultrasonic cleaner
- Ultrasonic cleaner sends sound waves to the metal surface
- The sound waves cause the chrome particles to vibrate at a high speed
- This vibration causes the bond between the chrome particles and metal to break down
- It causes the removal of chrome plating from the metal surface.
An ultrasonic cleaner is a safe and nonhazardous method for removing chrome plating from metals. However, ultrasonic cleaners are expensive and, therefore, not feasible for just one-time removal.
2.Vapor Degreasing
This process is known as degreasing because it does not involve scrubbing or water. It involves a solvent vapor, which is condensed. The vapor solvent strips off the chrome plating from the metal surface.
A significant disadvantage of this process is that the vapor solvents are highly toxic chemicals. These include propylbromide, perchloroethylene, and trichloroethylene. The optimal temperature range for this process is 40-65’C. A pressure of 25amps or less is maintained during the process.
3.Dry Ice Blasting
Dry ice blasting is a versatile treatment for removing chrome plating. It is because of its application in metals, plastics and rubbers. It uses a cold jet system to remove chrome from chrome-plated materials.
This is the best method for hard chrome coating and sensitive parts. The cold jet system targets the chrome-plated surface with pellets under high pressure. Different nozzles fire different pellets under various pressure ranges.
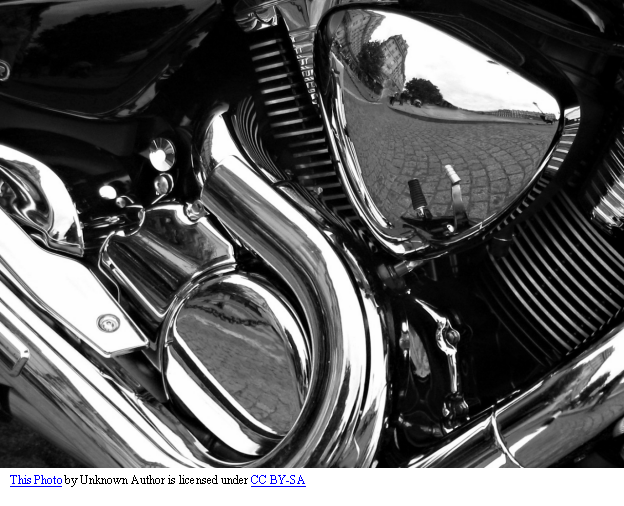
Finishing and Post-Processing
1.Cleaning the Metal
It is very important to finish the metal surface after removing chrome plating. For this, you can rinse the metal surface with a solution of baking soda. Baking soda neutralizes any chemical residues on the metal surface.
2.Polishing and Buffing
Suppose you want to use the metal further for anodizing or powder coating. In that case, you need to restore the metal’s original finish. For this purpose, you must polish or buff the metal surface after removing the chrome plating.
You can use several abrasive materials, such as fine-grit abrasives, for polishing. You can also use metal polish for this purpose. Buffing with a soft cloth also helps restore the original metal finish.
3.Protecting the Metal
It doesn’t stop at removing the chrome plating from the metal surface. Providing further protection to the metal from corrosion is also essential. You can apply paints and sealant to protect the metal surface from exposure to corrosion.
After removing the chrome plating, the paints and sealants create an extra protective layer for the metals.
Conclusion
This blog discusses various methods for removing chrome plating from metals. Chemical stripping uses acids and alkalis. Reverse electrolysis uses electric current. Mechanical methods use specialized equipment and techniques. Although chrome plating increases the durability and shine of a metal object, it needs to be removed in some cases.
Each method of removing chrome from metals has its own pros and cons. The selection of the best method depends upon the resources and expertise available. It also relies on the type of chrome plating. There are different techniques for decorative and hard chrome plating layers.
, Whatever technique or method you choose, always ensure that the necessary protective equipment and safety precautions are in place.