CNC machine process has been revolutionizing the manufacturing industry since decades. However, this technique cannot be exploited to its fullest unless you understand the basic parameters associated with them.
Feed rate and cutting speed are two important parameters that impact the efficiency and accuracy of the CNC machining and cutting process.
Both processes quite different from each other are technical in nature, Machinists need to gain ample knowledge about them to optimize various parts of the CNC machining processes.
This blog individually explains both concepts and then highlights the difference between the two.
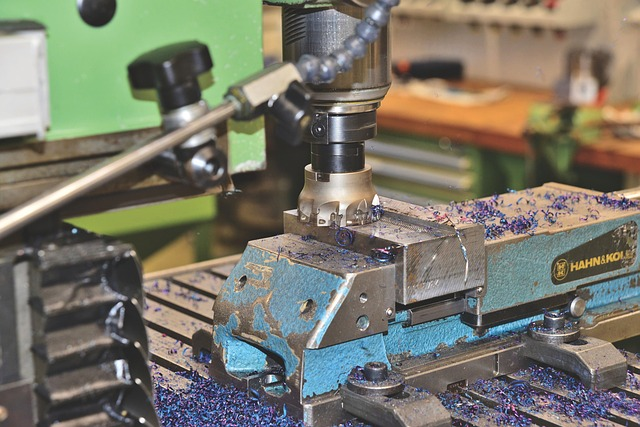
What Is Feed Rate?
Feed rate is the distance which the cutting tool travels towards the workpiece during one spindle revolution. It can also be the velocity with which the cutting tool advances towards the workpiece. The units of feed rate are inches per minute or millimeters per minute.
In case of boring or turning operations, the feed rate unites are different. They are inches per revolution and millimeters per revolution.
The feed rate varies with variations in factors such as:
- The surface pf the blank i.e. either the blank is made of steel, aluminum, wood or iron.
- The type of machine tools used in the process such as hss cutting tool, ceramic, cermet etc.
- Other factors such as CNC machining characteristics and surface finish also impact the value of feed rate.
Factors to Consider when Measuring the Feed rate
The feed rate depends upon the characteristics and features of the CNC machining process. The CNC machine tool influences the feed rate. Below are the characteristics that affect the feed rate:
1.Workpiece Hardness
Different materials have different properties. They are different in terms of hardness, brittleness, toughness etc. The optimum value of feed rate depends upon the material type.
Workpiece hardness has a lot to do with the optimum feed rate. In case of hard materials the feed rate value is low. It is because high speed can cause excessive tool wear and breakage.
Soft materials have less chances of premature tool wear. Therefore, the feed rate for soft materials is high.
2.Cutting Tool Material
Optimum feed rate also depends upon the cutting tool material type. Other factors such as the depth of the cut and the tool geometry determine the optimum cutting speed and feed rate value.
The cutter diameter is inversely proportional to the feed rate. Larger the diameter smaller the value of feed rate. The reason is that cutting tools with large diameter can move more material per revolution. It also reduces tool overload and increases tool life.
To achieve optimum feed, rate the tool should be sharp and well maintained.
3.The Rigidity of the CNC Machine tool
The optimal feed rate is the one that can be achieved without excessive vibration, deflection or tool chatter. For this purpose the rigidity of the CNC machine tools is very important. CNC machining with high horsepower, rigidity and various spindle speeds can result in high feed rate.
4.Fixturing of the Workpiece material
Fixturing of the workpiece material is very important. Good fixturing can result in stable process. Along with stability it also causes accuracy. This is more important during milling operations. Poor fixturing causes low feed rates. It also causes vibrations and chatter.
5.Surface finish
If you want to achieve good surface finish you have to keep the feed rates low. A high feed rate results in rough cut. For rough turning operation the feed rate value is 0.1-0.3mm/rev. For finishing operation, the feed rate value can be 0.01-0.05 mm/rev.
6.Productivity
Productivity achievement is a bit challenging. You can achieve high productivity with high feed rate but you have to compromise the cutter speed on surface finish. In some cases, you can increase the cutting speed by keeping the feed rate stable.
What Is Cutting Speed?
Cutting speed refers to the relative velocity between the cutting tool and the surface of the workpiece surface. It is also known as surface speed. Another definition called surface speed describes it as the linear motion or distance the cutting tool moves past as it moves on the workpiece surface.
The cutting speed determines various cutting parameters out of the Cnc Machine. These are:
- power consumption of the machine
- tool life
- Cutting temperature etc.
Different materials have different values of cutting speed. * High speed steel, carbon steel, aluminum, low carbon steel and plastics all have different values of cutting speed.
Two factors affect the cutting speed. These are:
- The diameter of the cutting tool
- The rotational speed of the spindle
When the cutting speed is higher it means that the relative velocity of the tool is higher on the workpiece surface. In short, higher cutting speeds, the tool is moving with fast speed. A low cutting sped indicates that the relative velocity of the tool with reference to the workpiece is low. It indicates a slow speed of the cutting tool.
In case of high cutting speed, the rate of material removed is also higher and vice versa.
When you setting the rate, you need to consider.
1.Cut Width
Cut width is also known as stepover and radial depth of the cut. When you view the cutting tool from above the cutting edges the total thickness you see refers to the cut width. It can never exceed hundred percent of the diameter of the cutting tool.
2.Cut Depth
Cut depth is an important aspect of the machining operations. It is represented by the symbol ‘ap”. It is actually a vertical distance between two parts on the workpiece. Among the two parts one is the machined surface and the other is the non-machined surface. The non-machined surface is the surface awaiting to be machined.
Cut depth as the name indicates determines how deeply the machine can cut during each feed. The following formula calculates cut depth:
ap= (dw-dm)/2
ap indicates the cut depth. The unit of cut depth is millimeters
dw indicates the diameter of the workpiece surface that is awaiting machining
dm is the outer diameter of the workpiece surface that has already been machined
The unit of both dw and dm is millimeters.
3.The strength of the cutting tool
The strength of the cutting tool plays an important role in determining the cutting speed. Strength of the tool is determined by the material constituting the tool and the tool geometry.
For example, Carbide cutting tools are considered to be harder and of superior quality as compared to steel cutting tools. For this reason, carbide tools can bear high cutting speed. They are also heat resistant. High and lower cutting speed steel tools wear down easily because they are abrasive in nature.
4.The Characteristics of the CNC Machine
Maximum cutting speed is influenced by the features and characteristics of the CNC machine as well. Two important features that impact cutting speed are the power of cnc machine and its rigidity. Best practice is to achieve maximum cutting speed without compromising on the surface finish and the cutting tool longevity.
Importance of Speed and feed rate in Machining operations
Several factors make optimal cutting speeds, speed and feed important in the machining operations. Among those the two most important factors are:
- The rate of material removed.
- The amount of material removed.
Both factors cutting speed and feed determine tool performance and longevity.
Both factors cutting speed and feed can be differentiated on the basis of an important factor. The name of that factor is “cutting temperature”. A high cutting speed feed temperature can reduce the tool life. It also increases surface roughness.
Certain materials give a lot of space for errors to occur. Consider for example aluminum and resin. They tend to hide the errors produced by speed and feed rate. These are actually soft material type. In case of harder materials such as titanium there is less room for error.
The difference between the cutting speeds and feeds is very important. In case of a slight difference between speeds and feeds the cutting tool can break immediately.
Speeds and feeds rate are important for the achievement of better surface finish. Even if you want a rough surface you need to give due importance to speed and feed rate. For example, if you want to achieve rough surface finish then conduct machine operations at high spindle speed and high tool rate.
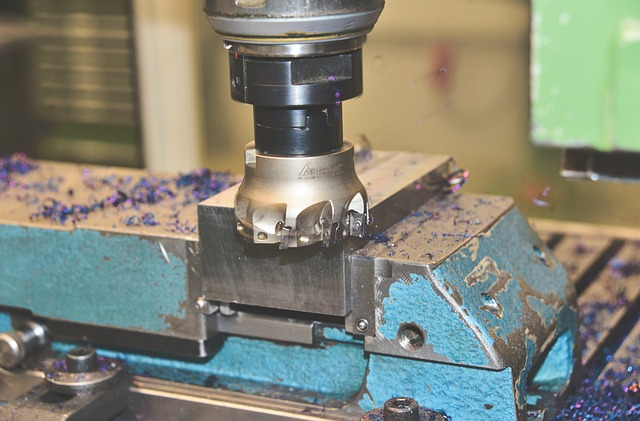
What is the Difference Between Cutting Speed and Feed Rate?
Now that you have known so much about speed and feed rate both you are able to better understand both concepts. However, there is still need to elaborate the difference between the two concepts. Following explanations make the speed difference clear:
Tool Movement
The way the tool moves along the workpiece also differentiates the two concepts from each other. The speed at which the tool moves across the workpiece is called feed rate. And the cutting speed is the speed at which cutting edge of the tool moves.
The unit of how fast the tool cuts is cutting speed. The measurement of how fast the tool moves across a given material is feed rate.
Cutting Temperature and Tool Life
As described before cutting temperature differentiates cutting speed and feed rate both. The extent of both factors’ effects on cutting temperature is the main difference between the two. However, it should be noted again that cutting temperature does hinder tool life and surface finish.
Surface Roughness and Scallop Marks
Being the main cause of surface roughness scallop marks are a mandatory appearance on CNC machined prototypes. Scallop marks are also known as feed marks. The frequency of scallop marks on the surface if any part is directly proportional to the feed rate. The higher the feed rate the more the appearance of scallop marks. This causes surface roughness.
How it differentiates cutting speed from feed rate?
Well it does
Because cutting speed does not have any impact on the presence of scallop marks. It does not impact the surface finish either.
Directrix and Generatrix
Although the names seem complicated but the concepts are easy to understand. A point or a surface that generates or creates a new shape every time when moved across a given part is known as a generatrix.
The directrix is the path along which the generatrix moves.
Do you know what is the main goal of machining?
It is the creation of different geometrical patterns or shapes with aesthetically pleasing surface finishes. Not to forget higher accuracy. Both generatrix and directrix are therefore important parameters in the machining operations.
But how does generatrix and directrix differentiate speed and feed rate?
The feed rate generates generatrix and cutting speed generates directrix.
Impact on Power and Cutting Force
Both cutting speed and feed rate differ on the basis of impact of power and cutting force of the CNC machine. The cutting speed does get influenced by the power and force of the CNC machining tool but the feed rate not.
Chip Direction
A chip is actually the sheared material. As the tool moves along the surface of the workpiece the sheared pieces or fragments which are actually small pieces of metals flow in orthogonal directions. These sheared pieces are called chips. The cutting speed does not have any impact in deviating the chip from its orthogonal direction.
However, the feed rate does cause deviation of the chip’s direction. The chip has two surfaces. One is a shiny surface with smooth finish and the other one is a rough surface.
Determination of Feed Rate and Cutting Speed
To determine feed rate and cutting speed various parameters need to be considered. Among them the most important parameter is spindle speed. Let’s know more about the parameters to accurately measure feed rate and cutting speed.
Non-Linear Path
Although the common assumption is that the feed rate follows a linear path i.e. straight movement or distance covered. Yet this situation is not same always. in some cases, the feed rate would be expected to follow a circular path or in the form of an arc.
During such situations the tool engagement is different at different areas. It is higher for internal corner and lower of external corners. To maintain circular motion as the angle of the tool engagement increases with the increase in the cut depth. This increase in angle causes the tool to adopt the non-linear path.
Cutting Velocity and Feed Rate Interaction
To accomplish the basic requirements of machining two motions, need to interact with each other. These are feed motion and the compression motion. The compressed motion is the motion that the cutting tool provides to the surface of the workpiece. It is in the form of relative velocity.
The compressive force helps in removal of the material from the upper surface of the workpiece. However, the feed motion needs to be applied to the surface in synchronization with the compressive force.
The collective impact or interaction of these two forces causes the removal of the material in the form of chips from the upper layer of the workpiece. The feed motion is provided to the cutter. The intensity of feed force is different for different milling operation.
The collective working of compressive force, feed motion and feed rate make up the basis for accurate machining operations.
Spindle Speed Limit
The speed of the cutter or spindle speed is the combination of the tool diameter and the surface feet per minute (SFM). The surface feet per minute varies with different material types.
However, in some cases speed calculation becomes faulty. In such cases the ideal case is to run the machine at its maximum speed. The required chip load for the diameter is maintained. All the optimal parameters of the machine are achievable at its highest or maximum speed.
Conclusion
Optimization of cutting speed and feed rate can lead to efficient working of CNC machine parts. This can further lead to the manufacturing of accurate machines parts with precise measurements and surface finishes.
Machinists and engineers need to pay a lot of attention to feed rate and cutting speed. In the absence of accurate implementation, the manufactured parts will lack proper finishing and measurements.